18Cr2Ni4WA鋼滲碳層邊界潤滑磨損特性
采用18Cr2Ni4WA鋼,在氣體滲碳爐中,碳勢為1.0%,920℃的條件下進(jìn)行5h滲碳,對(duì)試樣重新加熱淬火,并通過回火、冷處理等方法改變滲層中的奧氏體量。研究了滲層中的奧氏體在摩擦磨損過程中的相變行為及相變對(duì)金屬間邊界潤滑磨損特性的影響。
磨損是最常見的機(jī)械失效形式之一,長期以來,開發(fā)新型的耐磨材料和采用適當(dāng)?shù)奶幚硖岣吡悴考哪p壽命,一直是材料學(xué)的重要研究內(nèi)容。磨損是極復(fù)雜的失效過程,受材料自身特性、工件的工作環(huán)境、摩擦副的匹配、相對(duì)滑動(dòng)速度、應(yīng)力的大小與作用方式和工件表面狀態(tài)等諸多方面的影響,因此給研究磨損問題帶來很大困難。摩擦是不可缺少和不可避免的事情,人們根據(jù)需要來設(shè)法增大或減小物體間的摩擦,而磨損是摩擦導(dǎo)致的必然結(jié)果。生產(chǎn)中為減小機(jī)件的磨損,保證機(jī)械正常運(yùn)行,除要改善工件的工作環(huán)境、減小摩擦系數(shù)外,還要采用適當(dāng)?shù)牟牧稀DΣ吝^程中由于有熱量產(chǎn)生和相互間的作用力,因此機(jī)件常受高溫和應(yīng)力的作用,這種作用對(duì)材料的磨損特性有很大影響。金屬材料的磨損特性與其顯微組織、物相種類及各相所占的比例有很大關(guān)系,尤其是那些在摩擦過程中的不穩(wěn)定相,因其在摩擦?xí)r會(huì)發(fā)生相變或其他變化,這種影響就更大。此變化如何影響材料的磨損過程及耐磨性,始終是材料學(xué)者所關(guān)注的問題。奧氏體是最常見的室溫不穩(wěn)定的、且是鋼材中常存在的物相之一,研究它在摩擦過程中的行為是有重要意義的。本文采用18Cr2Ni4WA鋼,采用二維控制臥式氣體滲碳爐,在碳勢為1.0%和920℃的條件下進(jìn)行氣體滲碳5h,對(duì)獲得樣件重新加熱淬火,并通過回火、冷處理等方法改變滲層中的奧氏體量,在不同條件下進(jìn)行滲碳層與其它鋼材之間的金屬間臨界潤滑磨損試驗(yàn),來考察原奧氏體含量、應(yīng)力大小對(duì)材料耐磨性的影響,利用必要的檢測方法分析它在摩擦過程中的相變行為及其對(duì)材料耐磨性的影響規(guī)律。意在給證明目前頗有爭議的關(guān)于“奧氏體對(duì)耐磨性影響作用”問題提供一些試驗(yàn)依據(jù)。
1、試驗(yàn)內(nèi)容及方法
1.1、試樣制作
不同奧氏體含量試樣的制作:18Cr2Ni4WA鋼化學(xué)成分見表1。在二維控制臥式氣體滲碳爐中,碳勢為1.0%和920℃的條件下進(jìn)行氣體滲碳5h,滲層深度0.9mm,試樣為ML-10型磨料磨損試驗(yàn)機(jī)用的標(biāo)準(zhǔn)試樣,對(duì)獲得樣件重新加熱到780℃奧氏體均勻化后油淬,二次淬火的保護(hù)碳勢也為1.0%。將淬火后試樣通過回火、冷處理等方法改變滲層中的奧氏體量,工藝參數(shù)見表2。
表118Cr2Ni4WA鋼化學(xué)成分質(zhì)量分?jǐn)?shù) w(%)
C | Cr | Ni | W | Si | Mn | S | P |
0.21 | 1.52 | 3.45 | 1.01 | 0.22 | 0.44 | 0.003 | 0.010 |
表2ML-10磨損試樣淬火工藝和磨損試驗(yàn)外加載荷
工藝序號(hào) | 回火及冷處理溫度/℃ | 磨損試驗(yàn)外加載荷/Pa |
1 | 180 | 7.56×104 |
2 | 180 | 1.323×105 |
3 | 180 | 1.89×105 |
4 | -20 | 7.56×104 |
5 | -20 | 1.323×105 |
6 | -20 | 1.89×105 |
7 | -80 | 7.56×104 |
8 | -80 | 1.323×105 |
9 | -80 | 1.89×105 |
10 | -196 | 7.56×104 |
11 | -196 | 1.323×105 |
12 | -196 | 1.89×105 |
注:滲碳工藝為920℃,滲碳5h,碳勢1.0%,淬火工藝為780℃,均勻奧氏體化,油淬
對(duì)磨金屬盤的制作:將T10鋼鍛造后制成直徑為200mm、厚為10mm的圓盤,780℃均勻奧氏體化后油淬,200℃回火1h后進(jìn)行磨削加工,表面粗糙度Ra為0.16mm,硬度為60HRC。
1.2、試驗(yàn)方法
對(duì)上述各工藝獲得的試樣采用電解剝層分析法,跟蹤檢測滲碳層的碳含量分布、硬度分布和奧氏體含量及分布。
采用ML-10型磨料磨損試驗(yàn)機(jī),將磨料砂紙支撐盤換成經(jīng)上述處理的T10鋼金屬盤。進(jìn)行18Cr2Ni4WA鋼滲碳試樣滲碳層與T10金屬盤間噴油霧潤滑磨損試驗(yàn),試驗(yàn)時(shí),限定相對(duì)滑動(dòng)速度和相對(duì)滑動(dòng)距離,改變外加載荷的大小見表2,考察每一工藝的試樣滲碳層的磨損特性,同時(shí)用X射線晶體分析儀對(duì)每一次磨損表面的奧氏體量和奧氏體中的含碳量進(jìn)行檢測。奧氏體中含碳量檢測是通過檢測磨損表面奧氏體的點(diǎn)陣參數(shù),根據(jù)點(diǎn)陣參數(shù)與碳含量之間的相互關(guān)系計(jì)算得出。磨損量用失重法表示,失重量用TG328A電光分析天平測量。
2、試驗(yàn)結(jié)果
滲碳層不同處理?xiàng)l件下的顯微組織見圖1。
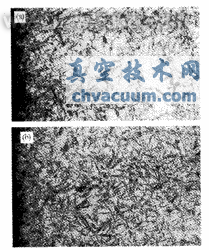
圖1 18Cr2Ni4WA鋼滲碳層不同處理?xiàng)l件下的顯微組織×250
(a)180℃回火,針狀馬氏體+75%奧氏體
(b)-80℃冷處理,針狀馬氏體+38%奧氏體
電解剝層分析檢測結(jié)果:滲層中的碳含量分布見圖2。滲層中的硬度分布檢測結(jié)果見圖3。不同處理工藝下,每層中的奧氏體量及分布檢測結(jié)果見圖4。
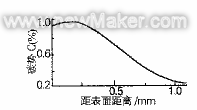
圖2 18Cr2Ni4WA鋼滲層中的碳含量分布
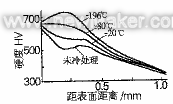
圖3 經(jīng)不同工藝處理的18Cr2Ni4WA鋼滲碳層硬度分布
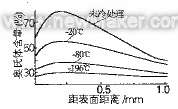
圖4 經(jīng)不同工藝處理的18Cr2Ni4WA鋼,電解剝層測得滲層奧氏體分布
磨損試驗(yàn)過程中,每次磨損后,試樣磨損表面的奧氏體量及奧氏體中含碳量的檢測結(jié)果:各種載荷下,磨損表面奧氏體量檢測結(jié)果見圖5。各種載荷下,磨損表面奧氏體中含碳量檢測結(jié)果見圖6。
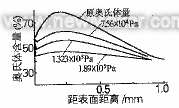
圖5 18Cr2Ni4WA鋼未冷處理試樣不同載荷時(shí)磨損表面奧氏體分布
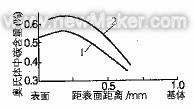
圖6 18Cr2Ni4WA鋼磨損時(shí)滲層中奧氏體含量的變化
1、原始奧氏體2.1.89×105Pa磨損后奧氏體
各種載荷和不同原始奧氏體含量下的滲碳層磨損試驗(yàn)結(jié)果:相同原始奧氏體含量及分布,不同載荷下的磨損試驗(yàn)結(jié)果見圖7。不同原始奧氏體含量在相同載荷下的磨損試驗(yàn)結(jié)果見圖8。未經(jīng)冷處理試樣磨損表面和電解剝層表面硬度跟蹤檢測結(jié)果見圖9。
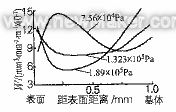
圖7 18Cr2Ni4WA鋼未冷處理試樣不同載荷下的磨損特性
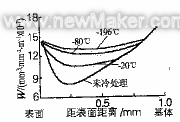
圖8 18Cr2Ni4WA鋼不同原始奧氏體量1.89×105Pa下的磨損特性
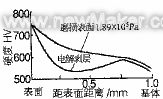
圖9 18Cr2Ni4WA鋼未冷處理試樣磨損表面和電解剝層表面硬度跟蹤檢測結(jié)果
3、試驗(yàn)結(jié)果分析
3.1、滲層中奧氏體在摩擦過程中的誘發(fā)馬氏體相變及影響因素
根據(jù)電解剝層與磨削剝層表面奧氏體量及硬度檢測結(jié)果(如圖5和圖9)可知,在摩擦磨損過程中奧氏體發(fā)生了相變。X射線晶體分析測定表面奧氏體相對(duì)含量時(shí),觀察兩者的奧氏體與馬氏體的衍射峰強(qiáng)度的變化情況,結(jié)果表明隨磨損試驗(yàn)載荷增大,相應(yīng)的奧氏體衍射峰強(qiáng)度降低,而馬氏體衍射峰強(qiáng)度增大,說明上述相變是馬氏體相變。由圖5進(jìn)一步可以看出,誘發(fā)馬氏體相變量的多少主要受兩個(gè)方面因素的影響,即原始奧氏體量和磨損時(shí)載荷(摩擦接觸面上的應(yīng)力)大小的影響。一般規(guī)律是隨原始奧氏體量增大、接觸表面應(yīng)力水平提高,摩擦誘發(fā)馬氏體相變量增大。這是由摩擦誘發(fā)馬氏體相變的驅(qū)動(dòng)力和相變阻力的相對(duì)大小決定的,原始奧氏體量較大時(shí),因淬火相變產(chǎn)生的壓應(yīng)力較小,奧氏體中的低碳區(qū)域較多,誘發(fā)相變的阻力較小,可能發(fā)生誘發(fā)馬氏體相變的區(qū)域增多,有利于摩擦誘發(fā)馬氏體相變,反之則不利于摩擦誘發(fā)馬氏體相變;另一方面,在外加載荷較大時(shí),因試樣與對(duì)磨鋼板的接觸面積保持不變,導(dǎo)致名義接觸面應(yīng)力水平較高,在相對(duì)摩擦滑動(dòng)時(shí),接觸面及其附近的應(yīng)力、應(yīng)變都較大,摩擦誘發(fā)馬氏體相變驅(qū)動(dòng)力較小,同時(shí)維持在誘發(fā)相變臨界驅(qū)動(dòng)力水平以上的微區(qū)域較多,使摩擦誘發(fā)馬氏體相變量增大。
3.2、摩擦誘發(fā)馬氏體相變對(duì)滲碳層磨損特性的影響
邊界潤滑磨損的特點(diǎn)是既有直接接觸的區(qū)域,又有被薄油膜分隔的區(qū)域,從磨損表面分析結(jié)果來看,具有粘著磨損、磨料磨損和表面微裂紋油楔剝落等三重磨損特征,反應(yīng)了這種磨損過程的復(fù)雜性。而奧氏體相變的產(chǎn)生,使磨損過程更加復(fù)雜,表現(xiàn)出其特有的性質(zhì)。奧氏體摩擦誘發(fā)馬氏體相變對(duì)滲碳層邊界潤滑磨損特性影響很大,誘發(fā)相變過程中,一方面使磨損表面及其附近硬度提高(如圖9),有利于提高滲碳層的耐磨性;另一方面,誘發(fā)相變吸收了材料變形和裂紋產(chǎn)生和擴(kuò)展的能量,使材料耐磨性得到提高。這個(gè)作用的大小受兩個(gè)矛盾方面的控制,即摩擦誘發(fā)馬氏體相變量的多少和外加載荷大小(接觸表面應(yīng)力大小)。摩擦誘發(fā)馬氏體相變量增多,對(duì)耐磨性提高的幅度增大;而摩擦誘發(fā)馬氏體相變需要有一個(gè)超過臨界應(yīng)力、應(yīng)變的應(yīng)力水平,在原始奧氏體量相同的情況下,應(yīng)力水平越高,誘發(fā)馬氏體相變量越大,有利于提高材料的耐磨性。但與此同時(shí),接觸面應(yīng)力水平提高,材料表面微觀變形增大,發(fā)生粘著的幾率增大,磨料嵌入磨損表面的可能性增大,形成表面裂紋油楔旋壁梁壓力增大,這些因素都將導(dǎo)致材料磨損量增大。上述兩個(gè)矛盾因素共同作用的結(jié)果決定了材料耐磨性的大小。從圖7的試驗(yàn)結(jié)果可以看出,在較低應(yīng)力水平下,原始奧氏體量大的耐磨性較小;在較高應(yīng)力水平下,原始奧氏體量大的耐磨性較大。由此可知,在確定選擇構(gòu)件材料的處理工藝、確定顯微組織和相組成時(shí),為提高其磨損使用壽命,必須首先考慮零部件的使用條件。只有顯微組織與磨損條件相匹配時(shí),才能達(dá)到預(yù)期的效果。
4、結(jié)論
(1)奧氏體相在邊界潤滑磨損條件下會(huì)產(chǎn)生摩擦誘發(fā)馬氏體相變。相變首先發(fā)生在低碳區(qū),相變量隨原始奧氏體量增大、摩擦接觸面應(yīng)力水平提高而增多。
(2)誘發(fā)馬氏體相變有利于提高材料的耐磨性,誘發(fā)馬氏體相變量越多,對(duì)耐磨性提高的幅度越大。
(3)不同的原始組織適合不同的磨損環(huán)境,在較低應(yīng)力水平下,原始奧氏體少的冷處理試樣耐磨性高;在較高應(yīng)力水平下,原始奧氏體多的未經(jīng)冷處理的試樣耐磨性高。
參考文獻(xiàn)
[1]劉喜明.摩擦磨損中的馬氏體相變及其對(duì)材料磨損特性的影響[J].金屬熱處理,1997(3):8~12.
[2]董嘉祥.氣體碳氮共滲層中殘留奧氏體對(duì)性能的影響[J].金屬熱處理,1983,(9):32~36.
[3]長春汽車研究所.工程材料〔M〕.1983:25.