基于SolidWorks和ANSYS的支架頂梁應(yīng)力分析
針對支架頂梁的結(jié)構(gòu)特點和性能要求,采用SolidWorks三維建模和ANSYS結(jié)構(gòu)性能分析相結(jié)合的方法,用有限元結(jié)構(gòu)分析方法模擬并獲取了支架頂梁的應(yīng)力分布數(shù)據(jù),找出了其危險截面位于支架頂梁與立柱連接處附近,提出了優(yōu)化結(jié)構(gòu)性能的改進意見,為進一步分析支架頂梁的結(jié)構(gòu)強度和優(yōu)化設(shè)計提供了理論依據(jù)。
液壓支架是煤礦綜合機械化采煤工作面的重要設(shè)備,其主要作用是支撐和控制工作面頂板,隔離采空區(qū),維護安全作業(yè)空間,以及推移工作面的采運設(shè)備。由于液壓支架結(jié)構(gòu)復(fù)雜,負載變化大,工作環(huán)境惡劣,有些部件在工作使用中經(jīng)常因過載而損壞,給煤礦安全生產(chǎn)帶來很大隱患。根據(jù) GB 25974.1—2010《煤礦用液壓支架 第一部分:通用技術(shù)條件》規(guī)定,液壓支架在出廠前應(yīng)進行強度試驗,但因其試驗只能檢測有限點的應(yīng)力狀況,一些應(yīng)力集中區(qū)域由于安裝應(yīng)變片困難而無法檢測其實際應(yīng)力大小。在此背景下,借助計算機有限元模擬技術(shù),對液壓支架的主要部件進行虛擬樣機模擬試驗,掌握總體及局部細節(jié)的應(yīng)力狀況,已逐漸成為強化試驗檢測手段,提高結(jié)構(gòu)設(shè)計可靠性,提高產(chǎn)品開發(fā)效率的重要途徑。筆者利用三維建模軟件 SolidWorks 和大型有限元分析軟 ANSYS,對支架頂梁進行三維實體建模及有限元應(yīng)力分析,并在模擬的基礎(chǔ)上,尋找其工作危險截面,對支架頂梁結(jié)構(gòu)的設(shè)計優(yōu)化和保證煤礦安全生產(chǎn)具有一定的理論指導(dǎo)意義和工程實際應(yīng)用價值。
1、三維實體建模
支架為某公司的產(chǎn)品,頂梁是由各種鋼板焊接而成的三維箱形結(jié)構(gòu),其與立柱的連接采用銷軸鉸接方式。筆者采用三維建模軟件對支架頂梁進行實體建模。ANSYS 軟件可建立簡單的二維或三維物理模型,但對比較復(fù)雜的工程實際問題,其三維建模能力較弱。因此選擇建模功能更加強大的 SolidWorks 軟件對支架頂梁進行實體建模,然后再將模型數(shù)據(jù)導(dǎo)入ANSYS 軟件中。
為了保證導(dǎo)入 ANSYS 后的模型能夠正確有效且無變形,在 SolidWorks 建模時要注意保持實體特征的獨立性,要求在創(chuàng)建實體特征時不能合并實體。此外,根據(jù)液壓支架試驗工況及支架頂梁受力情況,對支架頂梁進行結(jié)構(gòu)簡化,去掉對結(jié)構(gòu)強度影響較小的側(cè)板、圓角、倒角及小孔等輔助特征。模型創(chuàng)建成功之后,將零件圖保存為 .xt 格式,并將模型數(shù)據(jù)導(dǎo)入ANSYS 軟件。導(dǎo)入 ANSYS 后的支架頂梁三維實體模型如圖 1 所示。
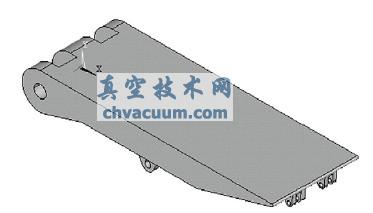
圖1 支架頂梁三維實體模型
4、結(jié)論
利用SolidWorks和ANSYS 軟件對支架頂梁進行三維實體建模和應(yīng)力數(shù)值計算,得到了在Von Mises準則下的主應(yīng)力分布,并得出以下結(jié)論。
(1) 利用SolidWorks和ANSYS 軟件可方便地獲取支架頂梁受載荷作用下的應(yīng)力分布,找出其結(jié)構(gòu)的危險截面,可以為支架頂梁的理論分析和實際應(yīng)用提供參考依據(jù)。
(2) 從結(jié)果分析中可知,支架頂梁最大等效應(yīng)力位置位于支架頂梁與立柱連接處。為了保證支架頂梁的可靠性,該位置應(yīng)采用強度較高的鋼材,如WH70高強度鋼,其附近區(qū)域應(yīng)選用先進焊接工藝和優(yōu)質(zhì)焊條。
(3) 借助計算機有限元模擬技術(shù),對液壓支架的主要部件進行虛擬樣機模擬試驗,掌握總體及局部細節(jié)的應(yīng)力狀況,可提前發(fā)現(xiàn)液壓支架結(jié)構(gòu)件的薄弱環(huán)節(jié),有利于提出改進和優(yōu)化措施。