固體滲碳技術概述
一、滲碳目的
滲碳就是向鋼的表面層滲體碳原子的過程。即把工件放入滲碳氣氛中在900-950℃加熱保溫,使鋼件表面層增碳的過程。
機械零件中,如凸輪、偏心輪、齒輪、活塞銷等類零件工作時表面經受強烈地摩擦,并承受著沖擊載荷,因此,要求表面硬、耐磨、心部應俱有良好的塑性和韌性。
如何滿足零件表面硬、耐磨心部又有良好的塑性韌性呢?這個問題,必須從材料使用和熱處理工藝方面分析研究,如果選用高碳鋼材進行淬火、低溫回火處理,雖具有高的硬度和良好的耐磨性,但塑性韌性較低,滿足不了要求。選用低碳鋼材料淬火后,雖具有高的硬度和良好的耐磨性,但塑性韌性較低,滿足不了要求。選用低碳鋼材料淬火后,雖具有良好的塑性韌性,但得不到高硬度和耐磨性的表面層,同樣滿足不了要求。而選用低碳鋼進行滲碳、淬火,則可以得到滿意的結果,這就是滲碳的目的。
二、滲碳用鋼
由于滲碳零件要求滲碳淬火后心部保持一定的韌性,宜用含碳量較低的鋼制造,一般含碳量在0.08~0.25%范圍。對于要求較高或較大截面的零件,含碳量達0.30%。由于低碳鋼強度較低,而且淬透性差,長時間滲碳晶粒易于長大,所以,重要零件(如汽車、拖拉機齒輪等)都用低碳合金滲碳鋼。合金滲碳鋼中常加入Cr、Ni、Mo、W、V、Mn、B和Ti等元素。各種不同合金元素對滲碳鋼有不同的影響,大數如下:
Cr、Mn、Ti等合金元素,它加入合金主要作用是增加滲碳鋼的淬透性,并使在淬火和低溫回火后表層和心部組織得到強化。
Mo、W、Ti、V、B等合金元素,它加入合金滲碳鋼中的含量雖然不多,特別是B的含量是極微的,僅為0.001-0.004%。Mo、W、Ti、V、Ti所起的主要作用是形成穩定的合金碳化物,阻礙奧氏體晶長大,并使合金滲碳鋼在淬火和回火后表層和心部組織得到強化。特別是增加表面耐磨性。微量的B能強烈地增加合金滲碳鋼的淬透性。
三、滲碳的一般原理和質量要求
鋼之所以能夠滲碳,是因為鋼在高溫奧氏體狀態,對碳具有相對大的溶解度(2.06%),鋼的滲碳就的借助這個原理。但是,并不是所有狀態的碳都可以被鋼表面所吸收,而只有活性碳原子才能被鋼表面吸收,被吸收的碳原子,在高溫狀態下在內部往外擴散,從而形成一定厚度的滲碳層。因此,滲碳過程中包括了分解、吸收、擴散三個基本過程。
(一)分解:
含碳化合物的分解,形成活形碳原子(用[C]表示):
2CO—→CO2+[C]
(一氧化碳)(二氧化碳)
CH4—→2H2+[C]
(甲烷)(氫)
(二)吸收:
高溫下活性碳原子與金屬表面接觸,被金屬表面吸收后,溶解于金屬基體或與金屬基體形成某種金屬化合物。
(三)擴散:
零件表面吸收(固溶)了碳原子后,表面含碳量增加,使零件表面與心部產生一定的碳濃度而促使表面碳原子逐步向心部擴散。
滲碳的結果取決于上述三個基本過程的關系。通過調整上述三個過程的關系,應滿足如下主要的滲碳層質量的要求:
⒈到達規定的滲碳層厚度(滲碳層厚度之計算,一般是從零件表層開始測量到過渡的二分之一處)。如滲碳層太薄時,在高負荷作用下,會使滲碳層壓穿,如滲碳太厚,也將影響滲碳零件的抗沖擊能力。
⒉滲碳表層含碳濃度應控制在0.8—1.05%范圍內。如含碳濃度過低(小于0.8%),則達不到所要求的高硬度,高耐磨性。如果含碳濃度過高(大于1.05%),則過剩碳化物較多,也使滲碳層強度,尤其是疲勞強度下降,特別當碳化物以針狀或網狀形式存在時由于馬氏體被這些脆性組織所割裂,對滲碳層強度起著特別有害的影響。
�、澈剂垦厣疃鹊淖兓�(也稱濃度梯度)要和緩,表層和心部之間的過渡區無明顯分界,以避免在使用過程中產生滲層剝落現象。
�、催^共析、共析層應占整個滲碳層厚度的60—70%,最低限度應不小于50%,這樣,使淬火后得到大致均勻的硬度,也不妨礙對滲碳層的最后研磨。
常用滲碳方法有:固體滲碳法和氣體滲碳法兩種。
四、固體滲碳
固體滲碳是一種應用最早的滲碳方法。
(一)滲碳劑的成份及其作用:
固體滲碳劑主要是由木炭粒和碳酸鹽(BaCO3或Na2CO3等組成。木炭粒是主滲劑,碳酸鹽是催滲劑。
木炭顆粒均勻,并要求3-6mm左右的占80%,1-3mm左右占20%左右,1mm以下的不大于1%,如果是大零件滲碳,大顆粒木炭應多些,小零件,小顆粒應多些。常用的滲碳劑成份如表1所示。
常用滲碳劑的成份
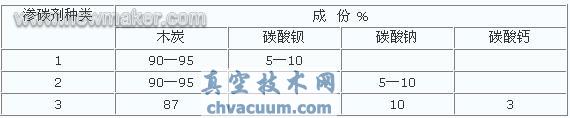
滲碳加熱時,炭與其間隙中的氧作用(不完全燃燒),生成一氧化碳。
2C+O2—→2CO
一氧化碳在滲碳條件下,是不穩定的,當它與鋼件表面接觸,便按下式分解得活性碳原子:
2CO—→CO2+[C]
活性碳原子被鋼件表面吸收,并向內部擴散。
整個反反應過程可用下式示意表示:
C+CO2—→2CO—→CO2+[C]—→工件
單獨用木炭進行滲碳,周期長,效果差,為了增加滲碳劑的活性,增加活性碳原子數量,一般加入一定數量的碳酸鹽作為催滲劑。催滲劑在高溫下與木碳產生如下反應:
BaCO3+C(木炭)—→BaO2+CO
Na2CO3+C(木炭)—→Na2O+2CO
2CO—→CO2+[C]
滲碳過程中,木炭受到了燒損,但催滲劑分解氧化物,在開箱冷卻時與空氣接觸,如按下方程式進行還原,這使催滲劑消耗大為減少。
BaO+CO2—→BaCO3
Na2O+CO2—→Na2CO3
為了提高催滲劑再生效果,在此介紹一種有效的方法,即將高溫下倒出來的滲碳劑,立刻用水噴灑(水的重量是滲碳劑重量的4—5%)。通過這樣的處理,碳酸鹽可得較完全的再生,其原因是:BaO+CO2—→BaCO3這個過程隨溫度下降而緩慢,如果在高溫下噴水,就能使BaO變成氫氧化鋇,而氫氧化鋇向碳酸鋇轉變不受溫度的限制。其反應如下:
BaO+H2O—→Ba(OH)2
Ba(OH)2+CO2—→BaCO3+H2O
噴水還可以減少木炭的燒損和促進少量甲烷發生,甲烷吸附在木炭的孔隙中,也能加速滲碳。
經過噴水處理的滲碳劑,加少量新滲碳劑便可使用。
(二)固體滲碳的操作方法:
�、迸渲茲B碳劑:
由于全新的滲碳劑催滲作用過于強烈,易導致零件滲碳后表層濃度過高和出現粗大或網狀碳化物。因此,一般新舊混合使用,其中新滲碳劑占20-40%,舊滲碳劑占60-80%。回收的舊滲碳劑應篩去灰粉后,才能與新滲碳劑配合使用。
⒉滲碳零件,滲碳前的準備處理:
要滲碳的零件,表面應盡可能潔凈,不應有嚴重銹斑及油垢,以免影響滲碳正常進行,造成零件滲碳后深度不均勻和產生軟點。
對于要求局部滲碳的零件,要認真進行防滲,常見的防滲方法有如下幾種:
①預留余量切除法:即在零件不應滲碳的部位,預先留出比滲碳層稍厚的加工余量,滲碳后再用機械方法把這部分切除。這種方法比較可靠,但材料和工時的損失較大,形狀復雜的零件,要切除余量也較困難。而且不能進行直接淬火。
�、谕苛戏ǎ河�1/3鉛丹和2/3氯化銅加上占兩種材料總量10-15%的松脂混合,溶于有機溶劑(酒精、汽油)中成糊狀,用毛筆涂于不需滲碳部位,厚度約0.7-1.0mm,干燥后再涂一層。
③鍍銅法:在不需要滲碳的部位用電鍍方法鍍上厚度為0.02-0.04mm的銅層,可以比較可靠的防止碳的滲入。
⒊裝箱:
滲碳箱一般用鋼板焊成或鑄鐵鑄成,滲碳箱不宜過大,其外形尺寸應盡可能適合工件的要求,箱子最好與爐底板架空,受熱均勻。
在生產中,往往發現這樣一種現象,由于滲碳箱過大,造成內外溫差大(滲碳劑是不良的熱導體),結果同一箱零件(外緣和中心)滲碳層極不均勻,故對滲碳箱的設計,必須考慮零件大小,形狀。同時應根據零件大小,滲碳時選用合適的滲碳箱,盡可能做到近似尺寸的零件同爐滲碳,盡量避免尺寸相差懸殊的零件同爐滲碳或小件用大箱滲碳。
零件裝箱時,在滲碳箱底部先鋪上一層滲碳劑(厚30-40mm),隨后即往箱內放工件,工件間距須保持10-15mm,工件和箱壁的距離則為20-25mm。
裝好一層工件后,鋪上一層滲碳劑并細心搗實,然后放上第二層工件,上下兩層工件之間滲碳劑厚度為15-25mm.。在裝工件的同時,應裝上試棒,試棒放置位置應盡可能的反映工件的實際滲碳情況。
在箱內放入最后一層工件后,上面放的滲碳劑厚度不得小于30-40mm。
裝箱好后,用耐火粘土(加上3-5%)食鹽加水調好進行封蓋,以防止在滲碳過程中滲碳氣體的逸出。
滲碳箱封好后,即在箱蓋上插入長試棒一根,同時也用耐火粘土封好試棒與箱蓋孔之間隙,如零件為低碳鋼,試棒材料應與零件相同,如零件為低合金或中合金鋼,試棒可用20#鋼制成,試棒直徑可用ф10-12mm,其插入深度為接近上層零件之間。
�、囱b爐與升溫:
零件可在低溫入爐并用分段升溫的方法。但對于連續生產,這種方法不經濟,故通常采用高溫入爐的方法。
由于固體滲碳時零件裝于密封的滲碳箱內,熱量要通過箱殼及箱內滲碳劑傳遞到零件上,如果控制不當,容易造成爐溫與零件實際溫度或箱內表層和中心的溫度差很大,零件滲碳深度不均勻。因此,
一般制定工藝時,均在爐溫升到820—850℃范圍保溫一段時間,使備部分溫度均勻一致后,才以緩慢的加熱速度升至900-930℃的滲碳溫度。
�、当貢r間:
零件在滲碳溫度下需要保溫時間視滲碳層深度要求而定,表2列出滲碳深度與保溫時間的關系。
滲碳溫度與保溫時間對滲碳層深度的影響
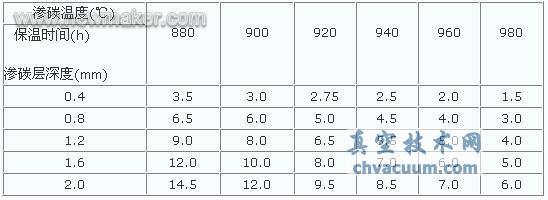
由于影響滲碳速度的因素較多如材料的化學成分,滲碳劑的配比和質量,以及爐子類型和滲碳箱的形狀,大小等等,故上列數據只能作為制定工藝的參考。
⒍出爐前的試棒檢查:
保溫完畢大約半小時抽檢試棒,可把試棒淬于水中,折斷后觀察斷口,或將斷面拋光后用4%硝酸酒精腐蝕,以檢查滲碳層所達到的深度,滲碳深度達到了技術要求則可出爐。如還未達到滲碳層深度,應適當延長保溫時間。
試棒檢查方法有以下幾種:
�、俳鹣鄼z查法:金相檢查法是一種可靠的測定辦法。它是將試棒正火后磨去端面碳層,然后進行研磨拋光,再用4%硝酸酒精溶液浸蝕,干燥后放在顯微鏡下觀察,從表面至中心部分,直到含碳約0.45%處為止,為滲碳層總深度,其中分過共析層(最外層)共析層(接過共析層)和亞共析層(接共析層)。含碳量均勻遞減為好。滲碳層總深度,可由金相顯微鏡上測出。若總滲碳層為1.2mm,其過共析層深約0.2-0.4mm,共析層0.4-0.6mm,亞共析層(0.45%C)深0.3-0.4mm。
�、诟g法:試棒按金相檢查法制成試樣,也用4%硝酸酒精溶液浸蝕,用肉眼觀察新面,發現一層灰色圓圈,用尺量一下這圓圈的厚度,即為滲碳層總深度。
�、勰繙y法:沒有金相顯微鏡,也沒有研磨拋光,浸蝕條件的情況下,就用目測法。目測法是將試棒從爐中取出,放在水中淬火,此時滲碳層應為高碳馬氏體組織,中心為低碳馬氏體組織。再將試棒于780~800℃在水中淬火一次,然后在壓機上壓斷(或敲斷),觀看斷口,因為滲碳層為高碳馬氏體,中心部分為鐵素體和低碳馬氏體,眼睛目測或10倍放大鏡觀看試棒,表層的細馬氏體層呈光亮的圓圈。由于表層是脆性斷裂:而中心有鐵素體,它是塑性斷裂,故表層斷口光亮,中心斷口不光亮。這樣估計總滲碳深度還包括含0.45%以下的部分,故此目測法的深度比金相法約深0.2—0.3mm。
試棒經過兩次淬火,都在水中冷卻,加之滲碳后的試棒表層與心部含碳量相差很大,淬火時產生很大的內應力,往往使滲碳層與心部部分分裂開來,如樹皮剝落一般,這樣更利于判斷滲碳層的深度。
�、房刂乒腆w滲碳表層含碳濃度的方法:
固體滲碳,由于零件密封于滲碳箱內,在滲碳過程中不能調節箱內氣氛,滲碳劑又直接與零件接觸,故滲碳作用強烈,滲碳后表面的碳濃度往往超過要求(特別是含有滲碳時易形成碳化物的Cr、Ti、Mo、等元素的鋼),對于一些抗彎和沖擊性能有較高要求的零件(如汽車齒輪等),將產生不利的影響,為了克服這一缺點,有關研究部門和工廠,通過試驗,摸索出如下降低滲碳表層含碳量的方法:
①把催滲劑的含量控制在一定的范圍內,用于低碳合金鋼的滲碳劑,含催滲劑2—4%;用于碳素鋼的滲碳劑,含催滲劑10-15%;舊滲碳劑與新滲碳劑之比例為3:1。
�、趯τ谝恍┖幸仔纬商蓟镌氐臐B碳鋼,除用上述配比的滲碳劑外,還采用降溫,保溫,擴散的方法,以盡可能減少零件表層的碳濃度。