基于UG與Moldflow的汽車門檻飾條工藝優化及模具設計
以汽車門檻飾條為研究對象,分析其結構和成型工藝,確定注塑模結構為一模兩腔。利用Moldflow 模擬分析,確定了澆口的最佳位置,分析了充填時間、熔接線、氣穴等。結合模流分析結果,利用UG 設計了分別裝在動模和定模的多個鑲塊的彎楔抽芯機構,斜頂側向抽芯機構、自動頂出機構等。結果表明:該方案結構合理、工作過程可靠、能有效地縮短塑件的生產周期。
隨著汽車行業的發展,人們生活水平日益提高,汽車逐漸成為了人們生活的一部分,人們對汽車的要求也越來越高,不僅要求汽車具有良好的使用性能,而且追求汽車具有良好的外形輪廓和舒適美觀的內飾。文章以某型汽車門檻飾條為研究對象,采用計算機輔助設計軟件UG 和有限元分析軟件Moldflow相結合的方法對其進行注塑模具設計,旨在達到減少試模、改模的次數,縮短產品的開發周期,節省成本的目的。
1、塑件結構與工藝分析
塑件三維結構如圖1 所示,塑件尺寸為1 773. 6 mm ×164. 9 mm × 109 mm,主壁厚3. 2 mm,最小壁厚1. 4 mm,材料為PP + EPDM + MD30。聚丙烯(PP)的主要特點是密度小,其力學性能如屈服強度、拉伸強度、硬度等均優于低壓聚乙烯;并有突出的剛性,耐熱性較好。通過對PP 進行彈性體改性(EPDM)和礦物質改性(MD30),可以在不明顯降低其它性能的情況下,大幅度提高聚丙烯的抗沖擊性能。
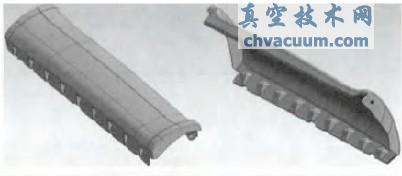
圖1 塑件三維模型
門檻飾條由曲面構成,有形狀不規則的孔及突起,左右不對稱。根據成型塑件一側壁上的方形通孔及兩端通孔的需要,需要側抽機構,另一側壁存在倒扣,要保證塑件出模,需要斜頂機構。為了提高生產效率及使模具進料受力平衡,保證模具的強度,采用一模兩腔,熱流道轉冷流道成型。
2、基于Moldflow 的模流分析
2.1、模型前處理
采用Moldflow CAD Doctor 導入塑件三維模型,去除對分析結果沒有影響的小圓角、倒角、臺階等結構,并將修復完成后的塑件導入Moldflow 2012 中,提高網格劃分的質量和效率。采用雙層面網格劃分,網格邊長取8mm。劃分網格后,模型網格匹配百分比和相互百分比達到92. 4% 和90. 5%。最后再修復自由邊、相交單元、縱橫比等缺陷,完成對塑件的網格劃分。
2.2、確定最佳澆口位置
根據塑件結構和實際經驗,預設了2 種不同的澆口位置方案,如圖2 所示。方案一采用三點進膠,可以減短流程,易于模具設計;方案二則采用六點進膠,相近的兩個澆口為一組,其作用相當于一個大的澆口,可以降低注射壓力,且相鄰兩澆口距離近,熔料溫度較高,澆口之間不會產生熔接痕。
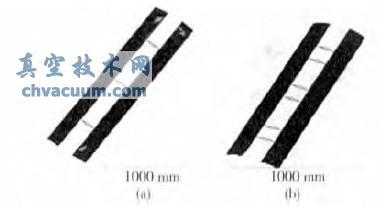
(a) 方案一;(b) 方案二。
圖2 澆口布置方案
通過對兩種方案添加澆注系統和冷卻系統的填充分析,得到如表1 所示的結果�?梢钥闯�,無論是充填時間、注射壓力、鎖模力和達到頂出溫度時間等,方案二的結果都優于方案一,因此選擇方案二的澆口布置方式進行下一步的深入模擬分析。
表1 方案參數比較
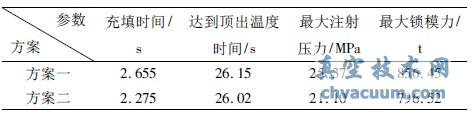
4、結論
文章綜合使用了UG 和Moldflow 軟件,針對汽車門檻飾條進行了詳細的成型工藝分析、模流分析和模具結構設計,找出了在注射過程中的熔接痕、氣穴等缺陷產生的原因,有效地保證模具設計的質量和效率,指導了實際模具設計和生產。